分享:00MW 超臨界電站鍋爐末級過熱器管爆裂失效分析
600MW 超臨界電站鍋爐末級過熱器管爆裂失效分析
晏嘉陵
(中國大唐集團 科學(xué)技術(shù)研究院有限公司 華東分公司,合肥 230088)
摘 要:通過宏觀檢驗、室溫拉伸試驗、金相檢驗、硬度試驗等方法對某600 MW 超臨界電站鍋爐末級過熱器管發(fā)生爆裂的原因進行了分析.結(jié)果表明:該爆裂管經(jīng)歷過長期超溫運行,組織老化嚴(yán)重,產(chǎn)生蠕變孔洞并連接形成裂紋,最終導(dǎo)致其在最薄弱的彎頭外弧面處發(fā)生爆裂.
關(guān)鍵詞:末級過熱器;爆裂;失效分析;長期超溫;組織老化;蠕變孔洞
中圖分類號:TK223.3;TG115 文獻(xiàn)標(biāo)志碼:B 文章編號:1001G4012(2017)06G0445G04
收稿日期:2017G02G28
作者簡介:晏嘉陵(1984-),男,工程師,碩士,從事電站金屬部
件監(jiān)督及結(jié)構(gòu)壽命評估工作,jialing_yan2009@163.com
FailureAnalysisonBurstingoftheFinalGStageSuperheaterTube
ina600MW UltraGSupercriticalBoiler
YANJialing
(EastChinaBranch,ScienceandTechnologyResearchInstituteCo.,Ltd.,ChinaDatangCorporation,Hefei230088,China)
Abstract:TheburstingfailurereasonsofthefinalGstagesuperheatertubeina600 MW ultrasupercriticalboilerwereanalyzedthroughthemethodsofmacroinspection,tensiletestatroomtemperature,metallographic
examination,hardnesstest,etc.TheresultsshowthattheburstingtubeexperiencedlongGtermoverheating,the
microstructurewasseriouslyaged,andcreepholesformedandconnectedtocracks,whichfinallyresultedinthe
burstingattheweakestpositionoftheelbowoutsidearcsurface.
Keywords:finalGstagesuperheater;bursting;failureanalysis;longGterm overheating;structureaging;
creephole
鍋爐4管(過熱器管、再熱器管、水冷壁管和省煤器管)是電站鍋爐的主要承壓和受熱部件.據(jù)粗略統(tǒng)計,鍋爐4管事故約占國內(nèi)鍋爐事故的2/3,是影響火電機組安全經(jīng)濟運行的最主要因素之一[1G7].隨著我國火電機組容量的不斷提高,汽水系統(tǒng)的壓力和溫度也相應(yīng)增加,在運行過程中出現(xiàn)了諸多問題.某電廠鍋爐末級過熱器管發(fā)生爆管事故,爆裂過熱器管材料為 GB5310-2008«高 壓 鍋 爐 爐 用 無 縫 鋼 管»中 的10Cr9Mo1VNbN(美 國 牌 號 T91)鋼 管,規(guī) 格 為
?38.1mm×7.96mm;爆 裂 位 置 為 由 西 向 東 數(shù) 第28排、由外向內(nèi)數(shù)第6根;過熱器管累計運行時間約6×104 h.該鍋爐型號為 SGG1918/25.4GM968,為超臨界參數(shù)變壓運行螺旋管圈直流、單爐膛、一次中間再熱、單爐膛四角切圓燃燒方式、平衡通風(fēng)、固態(tài)排渣、全鋼構(gòu)架、全懸吊結(jié)構(gòu)、露天布置、Π型燃煤鍋爐.過熱蒸汽出口設(shè)計壓力為25.4 MPa,設(shè)計溫度為571℃.筆者對爆裂末級過熱器管進行了檢驗和分析,查明了其爆裂原因,并給出了改進建議.
1 理化檢驗
1.1 宏觀檢驗
爆裂末級過熱器管爆口宏觀形貌如圖1所示,爆口位于鋼管彎頭背弧面,附近無明顯脹粗,爆口沿鋼管軸向長約30 mm.由于爆管后與其他過熱器管相互吹損,爆口邊緣部分位置吹損缺失,爆口附近部分未被吹損位置有明顯龜裂紋.
1.2 室溫拉伸試驗
在爆裂末級過熱器管上?。磦€拉伸試樣,使用CMT5105微機控制電子萬能試驗機進行室溫拉伸試驗,試驗結(jié)果?。磦€試樣的平均值,見表1.可見鋼管的抗拉強度和屈服強度均不能滿足 GB5310-2008對10CrMo1VNbN 鋼管的技術(shù)要求.
1.3 金相檢驗
在爆裂末級過熱器管爆口附近、爆口背面、距離爆口200mm 和500mm 的直管段位置分別截取金相試樣.試 樣 經(jīng) 磨 制、拋 光 和 化 學(xué) 侵 蝕 后 在 CarlZeissAxioObserverA1m 型金相顯微鏡下進行顯微組織試樣的.
可見爆口邊緣管內(nèi)壁有厚約0.32mm 的氧化皮,外壁氧化皮脫落嚴(yán)重,部分位置留有厚約 0.13 mm 的氧化皮,顯微組織晶粒細(xì)小,晶粒度在7級左右.爆口邊緣晶粒變形嚴(yán)重,附近有大量的蠕變孔洞,顯微組織為鐵素體+碳化物,馬氏體已經(jīng)完全分解,碳化物呈塊狀分布在鐵素體晶界位置.
圖3為爆口背面試樣的顯微組織形貌,可見管內(nèi)壁 有 厚 約 0.17 mm 的 氧 化 皮,外 壁 有 厚 約0.12mm 的氧化皮,顯微 組 織 晶 粒 細(xì) 小,晶 粒 度 在7級左右.顯微組織中大部分馬氏體分解成鐵素體+碳化物,部分碳化物在鐵素體晶界位置聚集長大成塊狀,部分碳化物仍彌散分布在基體中.
圖4為距離爆口200mm 處的顯微組織形貌,可見管內(nèi)壁有厚約0.20 mm 的氧化皮,外壁有厚約0.27mm 的氧化皮,顯微組織晶粒細(xì)小,晶粒度在7級左右.顯微組 織 中 馬 氏 體 已 經(jīng) 完 全 分 解 成鐵素體+碳 化 物,部 分 碳 化 物 在 鐵 素 體 晶 界 位 置聚集長大成 顆 粒 狀,部 分 碳 化 物 仍 彌 散 分 布 在 基體中.
圖5為距離爆口500mm 處的顯微組織形貌,可見管內(nèi)壁有厚約0.18mm 的氧化皮,外壁有厚約0.23mm 的氧化皮,顯微組織晶粒細(xì)小,晶粒度在7級左右.顯微組織中部分區(qū)域尚有馬氏體位相,部分區(qū)域馬氏體已經(jīng)分解成鐵素體+碳化物,細(xì)小的碳化物在鐵素體晶界位置聚集,部分碳化物仍彌散分布在基體中.
1.4 1.硬度試驗
利用 THBG3000MDX 型布氏硬度計在金相試進行布氏硬度試驗,結(jié)果見表2.硬度檢測結(jié)果顯示,爆裂末級過熱器管各個位置的硬度均低于 DL/T438-2016«火力發(fā)電廠金屬技術(shù)監(jiān)督規(guī)程»規(guī)定的下限值.
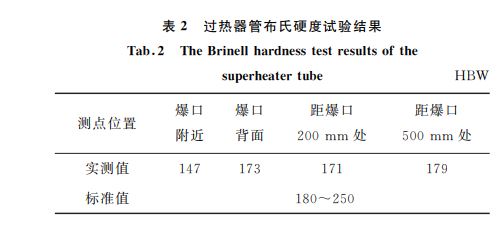
2 分析與討論
由以上理化檢驗結(jié)果可知,爆裂末級過熱器管的室溫抗拉強度、屈服強度和硬度均低于標(biāo)準(zhǔn)規(guī)定的下限值,爆口附近顯微組織中的馬氏體完全分解為鐵素體+碳化物,基體中的合金元素以碳化物的形式析出并在晶界位置聚集長大,爆口背面以及距離爆口200mm 和500mm 位置的顯微組織也均有比較明顯的老化趨勢.在低于600 ℃運行時,T91鋼中大量固溶的合金元素、彌散分布的碳化物和較高的位錯密度使其具有良好的抗蒸汽氧化性能和長時持久強度.而在超過600 ℃的條件下長期運行時,T91鋼中的合金元素會以碳化物的形式大量地析出、聚集和長大,顯微組織中的馬氏體加速分解,基體中的固溶強化、彌散強化和位錯強化作用大大減弱,進而導(dǎo)致材料的持久強度快速下降.
3 結(jié)論
綜合以上檢驗和分析可知,該超臨界電站鍋爐末級過熱器管經(jīng)歷過長期超溫運行,組織老化明顯,材料持久強度顯著下降.材料強度下降引起鋼管發(fā)生蠕變脹粗,產(chǎn)生蠕變孔洞并連接形成裂紋,最終導(dǎo)致鋼管在最薄弱的彎頭外弧面處發(fā)生爆裂.
4 建議
(1)增加溫度檢測點,加強受熱面鋼管的溫度監(jiān)控,防止超溫運行.
(2)擴大末級過熱器管的割管檢查范圍,確定管材老化趨勢,適時對末級過熱器管開展服役安全性評價,確保鍋爐安全穩(wěn)定運行.
(3)定期檢查彎頭氧化皮堆積情況,防止因氧化皮堆積造成管內(nèi)介質(zhì)流量不足而導(dǎo)致局部超溫.
更是在與螺母交界的螺紋根部產(chǎn)生了較大的單向應(yīng)力集中.螺紋根部不斷經(jīng)受疲勞產(chǎn)生疲勞裂紋,疲勞裂紋不斷擴展,當(dāng)?shù)蹉^螺桿剩余截面不足以承重時便會發(fā)生最終斷裂.
3 結(jié)論及建議
吊鉤螺桿斷裂屬于應(yīng)力集中造成的單向彎曲疲勞斷裂;吊鉤螺桿斷裂的主要原因是長期的不當(dāng)操作造成在斷裂處產(chǎn)生較大的應(yīng)力集中,在交變的彎曲應(yīng)力作用下最終造成疲勞斷裂.
鑒于以上分析,建議如下:①在起升貨物的過程中,必須要緩慢起升貨物,不能啟動太快,避免產(chǎn)生沖擊載荷;②經(jīng)常檢查吊鉤各部位,檢查和維護吊鉤組的結(jié)構(gòu)部件,如發(fā)現(xiàn)問題及時處理;③嚴(yán)格執(zhí)行操作要求,避免不規(guī)范操作,尤其是起吊重物時應(yīng)盡量避免橫向撞擊.
(文章來源: 材料與測試網(wǎng)-理化檢驗-物理分冊 > 53卷 > 6期 (pp:445-448))